

#SCANNERZ RACING PLUS#
In order to prototype and produce the modifications needed, including a Nylon 12CF GR86 hood vent, plus various other parts for its vehicle portfolio, the Toyota team has turned to the Fortus 450mc, F370, and F370CR 3D printers at Stratasys’ facilities in North Carolina and California, where they’ll be made before being shipped. Powered by a 2.4 liter boxer engine, the 231 bhp vehicle is being tuned by TRD for the GR Cup, a 14-race amateur, and affordability-focused race series, that’s set to launch next year in the US.
#SCANNERZ RACING SERIES#
Over the last 43 years, TRD has won championships in motorsports ranging from NASCAR’s Cup Series to NHRA Funny Car drag racing, establishing it as a trusted tuning body with significant motorsport expertise.Īs well as working on improving the performance of Toyota’s street cars, the organization is also responsible for supporting its motor racing exploits, hence it has been tasked with helping rebuild the GR86. Toyota’s latest forray into the world of additive manufacturing has seen its TRD division naming Stratasys as its new Official 3D Printing Partner. A close-up of one of the modifications TRD has made to the Cup Series GR86. At its Toyota Motorsport division, for instance, the company has not just unveiled plans to develop a new lightweight automotive material, but partnered with 3D Systems to create advanced technologies with high-end racing applications.
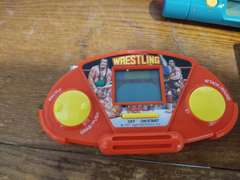

Since then, Toyota has (from what it’s said publicly) appeared to expand its 3D printing adoption further, by beginning to integrate the technology into its race cars. The firm has also had the 3D printing wing at the University of Waterloo named after it, in the wake of a $2.1 million (CAD) donation it made to the institution, to advance its R&D. These innovations were followed by further investments in research, including a partnership with DSM, in which Toyota co-developed Somos Taurus, a material with an automotive-friendly heat deflection temperature of 95☌. As long ago as 2015, the company worked with Materialise to develop an ultra-lightweight 3D printed car seat, before unveiling a new, shape-shifting ‘uBox’ car concept later that year, complete with customizable printed trim. However, in recent years, Toyota has also increasingly shown an interest in 3D printing, not just as a means of prototyping, but manufacturing end-use parts for its production cars. As you’d expect, this figure incorporates the sales of numerous different makes and models, many of which will have been made via traditional production processes. Headquartered in the Japanese prefecture of Aichi, Toyota is a multinational car manufacturer that, having sold over 9.6 million vehicles in 2021, remains one of the largest in the world. “By partnering with Stratasys, we are able to advance our manufacturing practices beyond what is currently possible, and really harness the possibilities of additive manufacturing for production parts.” Toyota’s GR Cup-spec GR86 race car. “Additive manufacturing has allowed us to quickly iterate, design and create parts for our race vehicles, in a way that would have been far more expensive or labor intensive through traditional manufacturing methods,” explains David Wilson, President of TRD. Using its partner’s technologies, TRD says it has managed to ramp up the R&D of these parts, while significantly reducing their cost of production. 3D printer manufacturer Stratasys has been named an Official 3D Printing Partner of Toyota Racing Development (TRD), the in-house tuning division of automotive firm Toyota.Īlready, in its new role, Stratasys has helped TRD develop several end-use 3D printed parts for the Toyota GR86, a sub-£30,000 production vehicle that’s set to be raced in the single-make GR Cup series.
